If you have come to this page and have been impacted we hope this page offers some brief guidance on the appropriate steps that should be considered to progress the recovery of your home or business.
Keystone Environmental do not perform remediation or building works but offer Indoor Environmental Consulting services for project management, water damage evaluations and or Post Remediation Validations PRVs.
Please note where emergency services, insurances or specific trades and the like are required, follow their advice before undertaking these works yourself where you are not suited to perform them.
What is considered a Catastrophic Event
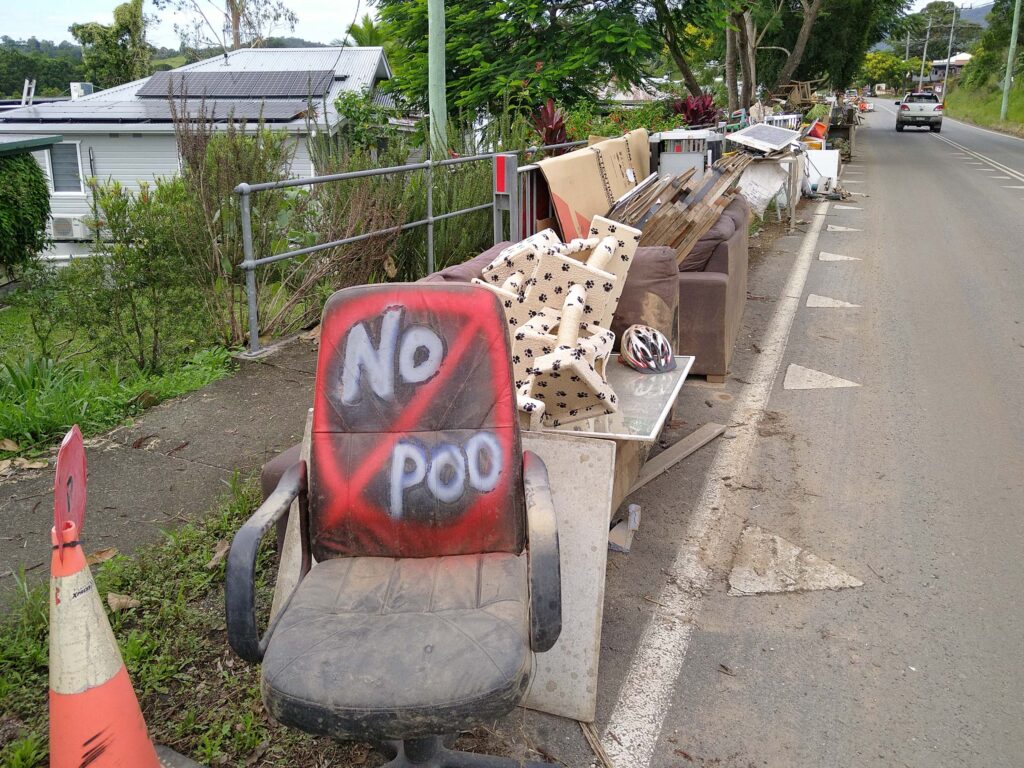
A catastrophic water damage event is an event that causes significant damage to property and contents due to ground water flooding, heavy rains, broken pipes, sewer backups, or other water-related issues. In these events water ingress may not only occur from the ground level but may bring with it ingress from above with roofing and drainage failures, hail damage or wind driven rain.
These events can be very costly, as they often require extensive repairs and restoration. The water can cause extensive structural damage to the home or business, as well as damage to electrical systems, furniture, and other personal items. Outside of fire smoke damage or meth contamination, mould contamination can be one of the most dynamic and pervasive risks when building materials become water damaged and are not attended to adequately with timely structural drying or physical source removal. Where flooding may be concerned depending on the category of water, bacterial. Viral and possibly chemical risks may also become a concern.
Ok, so what happens now?
To understand the appropriate response, its best to understand firstly what the levels of risk are regarding the level of water ingress or water loss. The following are categories and classifications taken from the respectable guidelines of the S500 and S520 of the Institute of Inspection Cleaning and Restoration Certification (IICRC). The actions recommended for each Classification or Category are our interpretation of how to apply these guidelines where no other regulation is applicable. There are no legislative mandates for these, but are a best practice outline.
For many of the recommended works we strongly suggest using qualified and accredited technicians under the IICRC, having certifications for Water Damage Restoration and Applied Microbial Remediation.
Definition of levels of Proofing
Post Remediation Evaluation – this is performed by the organisation who completed the sanitization, typically the remediation team themselves. These must include visual representations of the works performed and moisture mapping.
Complementary assessment tools such as Adenosine triphosphate or A.T.P surface swabs can be used to get a relative number or protein or enzyme detection tool with colour indicators. A.T.P. protein and enzyme technologies are a great, fast and informative screening tool to evaluate that the work that has been performed meets a desired quality control outcome. Samples may also be taken for fungal and or bacterial analysis. However, these tools and methods should not be considered as a validation.
Post Remediation Validation occurs by using a more robust method of testing for indicator organisms in the scenario of a Category event for quality assurance. This process includes an independent third party assessment of the sanitisation and mould remediation. The Indoor Environmental consultant shall be independent from those who performed the remediation works to offers a greater confidence that all due care was taken regarding bacterial decontamination and fungal remediation. A validators role is to offer greater confidence and value beyond what the other party performing evaluations might not otherwise. For this reason ATP or other real time monitoring equipment cannot define a best practice evaluation. A PRV must include a visual inspection by the validator, moisture mapping of all affected building materials that remain, microbial sampling of surfaces that were directly impacted or associated risks with photographic images and documentation outlining satisfaction or recommendations for further works to be performed. Bacterial samples taken shall be analysed by a laboratory analysing for indicator organisms as a minimum E.coli or best practice faecal coliforms (includes E.coli) and Enterococci. Fungal analysis of air and surface should include non-viable sampling methods and may include culturable methods.
The keys steps from damage to recovery
Step 1: Consider safety
It is crucial that all safety hazards be identified and eliminated immediately. It is the responsibility of all parties involved, from contractors to occupants themselves, to provide for the health and safety of everyone involved. This includes consideration of chemicals used and potential adverse health effects. All building materials must also be inspected for asbestos prior to removing any mould affected components and managed accordingly. Appropriate care should be taken where specific trades may be required regarding different hazards that should only be managed by them. A notable consideration can include electrical or engineering risks for example. It may also be notable that within certain jurisdictions the affected premises may become classified as a construction zone.
Commonly asked questions – answered
Where:
- Porous building materials have remained damp for greater than 48hrs consideration for strip out should be a minimum of 600mm above the tide height.
- Category 3 water has entered a cavity access must be gained from at least one side. If water proofing has to be damaged all associated areas of the water proofing system should also be removed.
- Tiles are adhered to damp porous materials these shall be removed.
- Tiles have been impacted and have become drummy or cracked, these should be removed.
- Engineered timber such as MDF or particle board that have been structurally or fungally compromised will require removal.
- Bracing ply is on both sides of a wall, consultation with relevant trades should be had to allow safe and effective access to the cavity.
- Category 3 Class 3 and 4 events have occurred floor coverings should be removed to allow adequate structural drying to occur.
These are generalized comments and individual sites and policies may not suit these responses.
Step 2: Report, inspect and record
Once step 1 has been established it may be time for occupants or owners to inform relevant parties including insurances or emergency services if not already performed in Step 1. Record everything related to the damaged event and begin to catalogue. For professionally engaged parties a thorough scope of work must be completed, in order to achieve this, properly assess and record the extent of water migration, including a moisture map. Additionally, the amount of moisture absorbed by materials must be determined. Once the drying process begins, progress must be verified and monitored at each inspection, with appropriate records kept. It is also beneficial to identify and report any pre-existing water damage or mould that is not related to the reported incident.
Note: the following steps may only rightfully be performed by suitably qualified persons more strictly than Steps 1 and 2.
Step 3: Prevent further damage
Understanding the type of water damage mentioned earlier and after the initial inspection to assess the extent of moisture intrusion and potential for water damage, it is essential to take immediate action to stop further damage. This may include removal of building materials, where asbestos or other risks are suspected, this should be left to appropriate trades. then affected materials and areas should be contained prevent cross-contamination. If a water damage claim is filed and the property has extra mould, preventive measures should be taken to resolve the issue, and it should be recorded and reported right away. If the mould suggests a larger problem, photographs and recordings should be taken and we should be contacted right away to discuss the best course of action. To prevent the spread of mould, affected areas should be encased and sealed with plastic or a good containment chamber should be created under negative or positive pressure depending on the application, where indecision for this occurs consult the engaged Indoor Environmental Consultant for guidance.
Step 4: Remediation and structural drying
For materials that have been contaminated and can be restored, contractors must adjust their drying methods based on the individual job site. Generally, if the water contamination is categorized as 1, the item should first be dried, re-evaluated, and then cleaned. If the water is categorized as 2 or 3, cleaning should be done first and then drying should follow. Structural drying using air movement should not commence until contaminated materials removed and containment is implemented.
Step 5: Proofing
Document thoroughly the works that were performed with images, moisture mapping and relevant comments. Depending on the type of loss as mentioned above different levels of proofing may be applied. These being the PRE or PRV mentioned earlier. Once evaluated criteria have been satisfied containment and controls may be removed and the building be handed over for reinstatement.